Our Lean Waste Identification dashboard has been updated on the Lean Launch Pad. This month over processing was leading ahead due to people just not storing things in the right place in the first place causing double handling and the potential to cause defects to the materials.
Over processing in Lean manufacturing refers to the act of doing more work, using more resources, or adding unnecessary complexity to a process beyond what is required to meet the customer’s needs or deliver a quality product. It can be reduced or eliminated by clearly defining the steps in the Standard Operating Procedures and Work Instruction and optimising them.
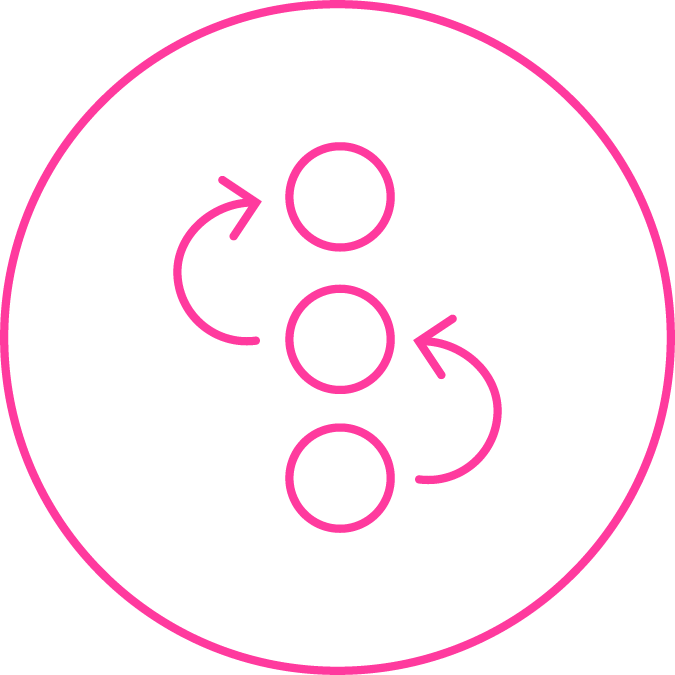
How to eliminate over processing:
- Have a clear understanding and communication about the customer’s requirements.
- Have a clear schedule and work plan.
- Complete a Value Add and None Value Add analysis for each activity and develop a Standardised Work method for the entire process. This should be done in an iterative manner for the entire process flow as more activities might get added due to changes in customer requirements.
- Establish clear quality standards and keep to them.
- Keep it simple by eliminating complexities that arise out of excessive documentation, instructions, manuals etc.
- Establish the final standard and move on.
- Automate the process steps where possible to reduce or eliminate the chances of over processing.
- Remember that any changes should be signed off using the change order.